
Two prominent mobile gadget insurers give their view on the need for grading refurbished smartphones
The insurance industry also has a vested interest in the refurbished industry, with both Bastion Insurance and Pier Insurance providing gadget insurance for technology products, including refurbished products.
How does the grading of refurbished phones impact the insurance sector?
John Fannon, sales director, Bastion Insurance:
Looking at programmes such as our Devicecover product, with which dealers will be familiar, grading here is vitally important to us. That’s because we would only ever supply an A-grade replacement to a Devicecover customer and therefore need to be certain that A-grade means a device indistinguishable from new.
In a way, this binary choice around A grades makes things simple for us. In other words. if you can’t tell whether its new or not, then it’s an acceptable A-grade, plain and simple. That is much easier than a typical woolly situation in which a debate occurs over whether something is a low-B or high-C grade, because that then becomes subjective and will vary from person to person.
Toby Stubbington, managing director, Pier Insurance: Given that the insurance sector purchases second-hand and refurbished phones, and is an important part of the circular economy, having trust and consistency in grading methodology is important.
What challenges are there for insurance companies and how does it impact policies?
Fannon: The main thing to get across to suppliers is to ensure that A-grade means A-grade. Furthermore, it needs to remain at that A-grade standard and not slip back to B-grade when we turn up the volumes and then see some lower-quality devices slipping into place to fulfil a volume order. In terms of impacting policies, let’s not forget that the main purpose of insurance is to put the customer back into the position they were in before an incident occurred, and if we were to supply badly graded handsets that were poorer than the one the customer had previously owned, then we would not be fulfilling that key requirement.
Stubbington: We work closely with partners to ensure a consistent understanding of grading, but also undertake quality assurance at various points in the device’s journey to ensure a consistent and excellent customer experience. We are conscious to ensure that parts used in any devices purchased are correct and the quality of any workmanship is of a sufficiently high level.
Do you believe it is possible for there to be an industry standard in place for the mobile industry?
Fannon: I think it’s possible for the A-grade category using the very simple yes-or-no definition that is mentioned above. However, when you start to sub-divide into Bs and Cs – and then in some cases B+ and so on – then it all gets vague and harder to calibrate across the industry as one man’s B-grade is another man’s C+. This gets even more complex when you move out of retail and into the refurbishment market and the parts-harvesting market.
Stubbington: Anything is possible. Consistency of measurement and grading would take friction out of the supply chain, but there are multiple issues to implement including: who sets the rules? How are these rules governed and audited? Is it possible to have consistency internationally? What parts are allowed to be used for which grading? Does a clear distinction need to be made between second-hand, refurbished and remanufactured? How is tech used to assist in grading? Would organisations or people need to be certified in order to grade?
How can this be achieved?
Fannon: I think that from a retail point of view, there should never be more than three grades, and then we can keep things simple with more definitive categorisation. To expand on this, I believe if we just used A, B and C, then you would either have a pristine and immaculate phone, or one with light scratches that cannot be seen from, say, more than arm’s length away, or one that is heavily marked – and that’s it. It goes without saying that all the handsets need to be fully operational and guaranteed.
Stubbington: Quality and safety standards have been applied in many industries, driven by government, public sector organisations or the trade itself. It is likely that the industry would have to galvanise around a pressing need for consistency of grading and certain organisations would sponsor creation of the grading system.
This could involve the formation of a small team with defined actions from different organisations to create, firstly, a framework that would be socialised and applied on a voluntary basis to develop more consistency over time; and secondly, once there was sufficient adoption of this framework and the feedback was positive (in terms of consistency), it could be further formalised and checked.
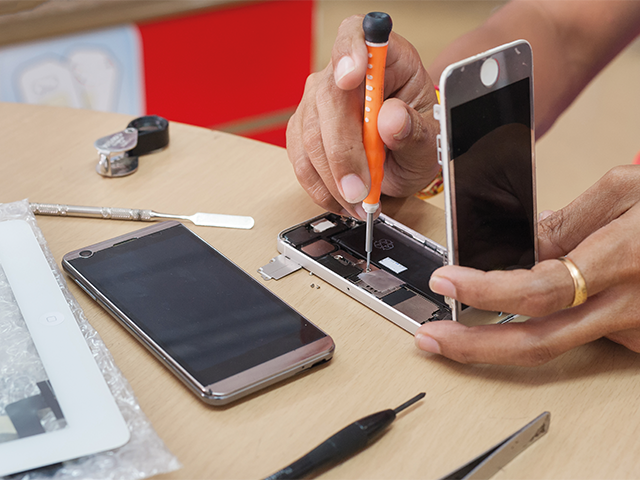
Why do you think there isn’t a standard in place now?
Fannon: Because it is being overcomplicated by many sub-grades. For example, I have no idea what constitutes a D-grade, so why have it? Perhaps the industry could get together and agree to share the same common high-resolution photographs that they could all use on their websites to give the exact same examples of an A, B and C grade handset, and then the customer or dealer would know what to expect when they receive the goods. This could then be used as a ‘grading standard’ that suppliers would sign up to and agree to stick to.
Stubbington: So far, grading has evolved as the sector has grown, and standards have been interpreted and set by multiple groups of parties. Setting consistent standards is generally achieved top-down, not via peer consensus, so this will have also made it harder to achieve. Finally, businesses and their people are focused on their other priorities.